Introduction to Telecentric Lenses
An important goal in machine vision applications is taking measurements in a consistent, accurate, and precise manner. This can include measuring the dimensions of manufactured parts to guarantee they are within the design tolerance, or measuring the width of electric tracks in a PCB. For these applications, telecentric lenses can deliver a high level of precision.
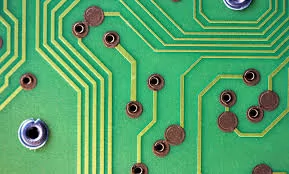
Images from a Telecentric Lens
A conventional image created by a lens will present a magnification of the object that will depend on the distance between the object and the lens. So, objects that are closer to the lens will create a larger image than objects farther away. This magnification (added to other aberrations as distortion) will affect how a machine vision will measure a particular object.
So if you are measuring the dimensions of tracks’ width (as in our previous example), and the PCBs are not aligned exactly the same or they are displaced a little bit from your optical system, they can create measurement errors due to these changes in magnification.
With a telecentric lens, these magnification errors are eliminated. This is because the image created by a telecentric lens has a magnification that is constant regardless of the distance between the object and the lens. In basic terms, a telecentric lens creates an orthographic image of our object.
An orthographic view is a two-dimensional representation of an object, kind of like drawing just the side-view of an object. So, the orthographic view of a cylinder would look like a square from the side-view and as a circle from the top-view. The way we create an orthographic view is by drawing parallel lines that are perpendicular to the view that we are observing. As shown in fig. 2.
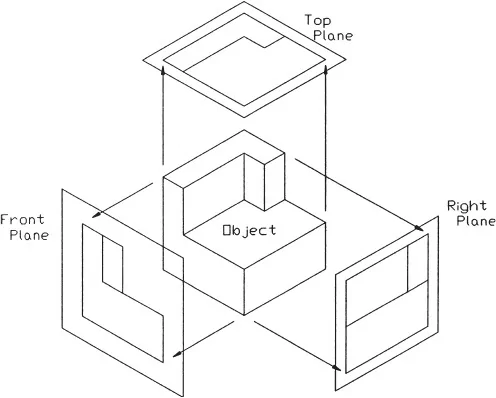
So how does a telecentric lens achieve this? A telecentric lens projects all its chief rays parallel to the optical axis. In other words, it can only receive light that is perpendicular to the lens. You can imagine a telecentric lens as a lens with a very narrow field of view.
So two objects, one in front of the other, would appear to be side by side on a telecentric lens. As a matter of fact, it would be almost impossible to tell which object is in front of the other. This makes taking measurements more consistent and less prone to errors. As shown in figure 3
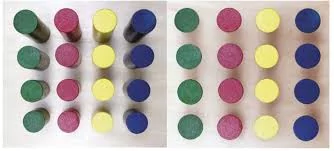
Principles of Telecentric Lens Design
A very common telecentric lens design is a double-telecentric system. In this configuration, we have a front optical element whose entrance pupil is located at infinity and its stop is placed at the lens’ back focal length.
We can also use a back optical element whose exit pupil is located at infinity and its front stop is placed at its front focal point (we basically place the second lens stop at the same location as the front element’s stop). In figure 4 we show a double telecentric configuration designed for one of our clients. Lenses of this type are used in chip manufacturing lithography systems.
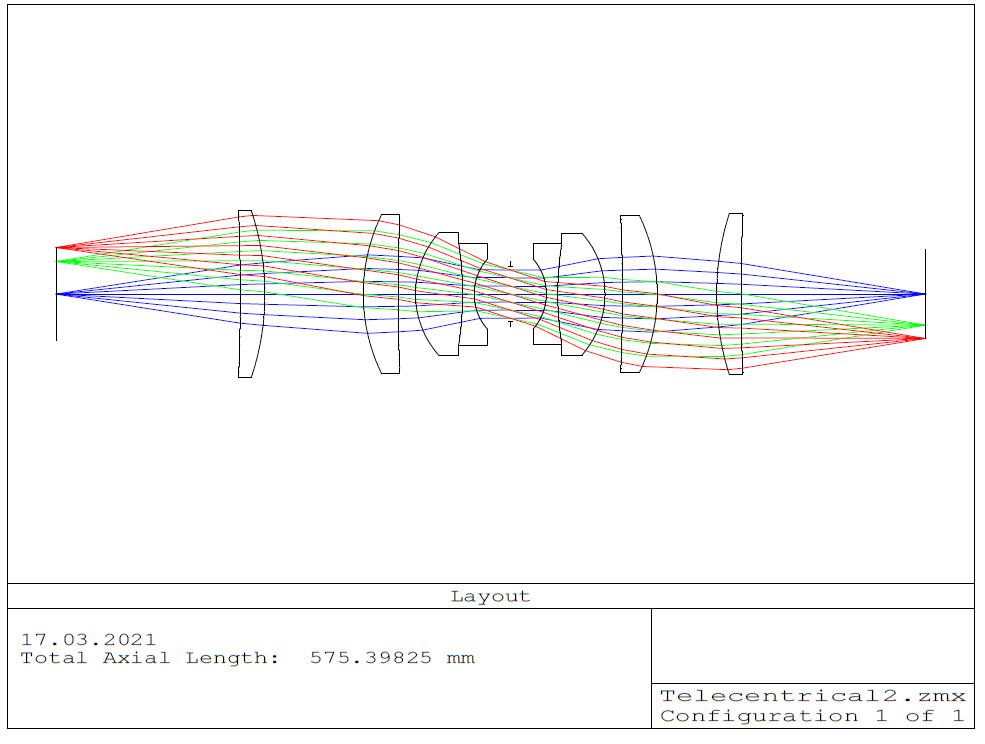
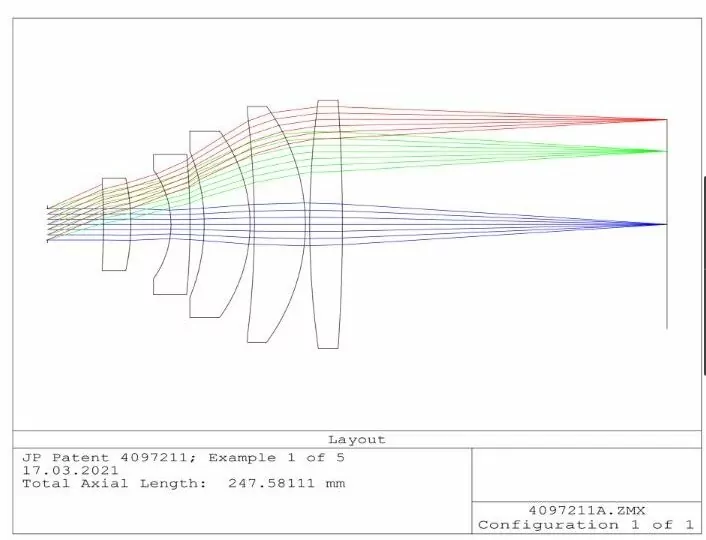
Key Applications in Machine Vision
Telecentric lenses play a crucial role in machine vision systems, where precise and accurate imaging is paramount. Here are some key applications where telecentric lenses excel:
- Dimensional Measurement and Inspection: Telecentric lenses are extensively used for dimensional measurement and inspection tasks where accuracy is critical. Their unique ability to maintain consistent magnification regardless of object distance ensures accurate measurements of objects’ dimensions, irrespective of their position within the field of view.
- Metrology and Quality Control: In industries such as automotive, aerospace, electronics, and manufacturing, telecentric lenses are employed for metrology and quality control applications. They enable the precise inspection of components, detecting defects, variations, or deviations from specified tolerances with high reliability.
- Particle Sizing and Analysis: Telecentric lenses are valuable in particle sizing and analysis applications, particularly in fields like pharmaceuticals, materials science, and environmental monitoring. They facilitate accurate determination of particle sizes and distributions, crucial for quality control and research purposes.
- Edge Detection and Surface Inspection: Telecentric lenses are ideal for edge detection and surface inspection tasks, enabling the detection of fine details and defects with high precision. They are used in applications such as detecting scratches, dents, or imperfections on surfaces of components or products.
- Barcode Reading and OCR (Optical Character Recognition): Telecentric lenses are employed in barcode reading and OCR applications for reliable and accurate data capture. Their ability to maintain consistent magnification ensures that barcodes and characters are accurately identified and interpreted, even in challenging environments with varying distances and angles.
- Alignment and Positioning: In manufacturing processes that require precise alignment and positioning of components, telecentric lenses are invaluable. They ensure accurate alignment of objects by providing distortion-free images with consistent magnification, aiding in tasks such as part positioning, alignment verification, and robotic guidance.
- Wafer Inspection in Semiconductor Industry: Telecentric lenses are used in semiconductor manufacturing for wafer inspection, where they enable the detection of defects and anomalies on wafers with high precision. Their distortion-free imaging capabilities ensure accurate inspection results crucial for maintaining the quality of semiconductor devices.
Designing for Precision and Accuracy
Designing telecentric lenses for precision and accuracy requires careful consideration of several optical and mechanical factors to ensure optimal performance. Here are some key aspects involved in the design process:
- Telecentricity: The primary characteristic of telecentric lenses is their ability to maintain a telecentric image space, where all object points are imaged with parallel chief rays. Achieving true telecentricity is crucial for accurate measurements, as it eliminates perspective errors and ensures consistent magnification across the entire field of view. Designing the lens elements and aperture configuration to achieve telecentricity is a fundamental aspect of the design process.
- Optical Aberrations: Minimizing optical aberrations such as spherical aberration, coma, and distortion is essential for maintaining image quality and accuracy. Telecentric lenses are often designed with complex optical configurations, including multiple lens elements and specialized coatings, to minimize aberrations and achieve high-resolution imaging.
- Uniform Illumination: Ensuring uniform illumination across the entire field of view is critical for accurate imaging and measurement. Telecentric lenses may incorporate optical elements or mechanical features such as apodization filters or diffusers to achieve uniform illumination, particularly in applications where lighting conditions can vary.
- Working Distance: Designing telecentric lenses with adjustable or fixed working distances allows for flexibility in various imaging setups. By optimizing the lens design for specific working distances, designers can ensure optimal performance and accuracy in different application scenarios.
- Depth of Field: Balancing depth of field with telecentricity is essential for maintaining sharp focus and accuracy, particularly in applications where objects may have varying heights or depths. Designing the lens optics to provide sufficient depth of field while preserving telecentricity requires careful consideration of aperture size, focal length, and other parameters.
- Mechanical Stability: Telecentric lenses must be mechanically stable to maintain precise alignment of optical elements and prevent image distortion or degradation. Designing robust lens barrels, mounts, and focus mechanisms that minimize mechanical vibrations and ensure stable positioning is crucial for achieving consistent and accurate imaging results.
- Calibration and Testing: Rigorous calibration and testing procedures are essential to verify the performance of telecentric lenses and ensure accuracy and precision in real-world applications. Designers employ advanced metrology techniques and calibration standards to validate optical performance parameters such as magnification, distortion, and telecentricity, ensuring that the lens meets or exceeds specified accuracy requirements.
By addressing these design considerations and optimizing the optical and mechanical characteristics of telecentric lenses, designers can create precision instruments capable of delivering accurate and reliable imaging for a wide range of machine vision applications.
Case Studies: Telecentric Lenses in Industry
Let’s explore two case studies showcasing the practical applications of telecentric lenses in different industries:
1. Automotive Industry: Dimensional Measurement and InspectionBackground: In automotive manufacturing, ensuring the precision and accuracy of components is crucial for maintaining product quality and safety standards. Dimensional measurement and inspection processes are employed extensively to verify the geometry and tolerances of various automotive parts, such as engine components, brake systems, and body panels.
Application: A leading automotive manufacturer implemented telecentric lenses in their dimensional measurement and inspection systems to enhance accuracy and efficiency. These lenses were integrated into automated imaging systems deployed along production lines to inspect critical components for dimensional accuracy, surface defects, and alignment.
Benefits:
- Telecentric lenses enabled precise and distortion-free imaging of automotive parts, ensuring accurate measurement of dimensions and tolerances.
- The telecentric imaging setup eliminated perspective errors and magnification variations, resulting in consistent and reliable measurement results across the entire field of view.
- By automating the inspection process with telecentric lenses, the automotive manufacturer significantly reduced inspection time and improved production throughput without compromising on quality standards.
2. Electronics Manufacturing: PCB Inspection and AlignmentBackground: In electronics manufacturing, printed circuit boards (PCBs) are subjected to stringent inspection and alignment processes to detect defects, verify component placement, and ensure optimal soldering quality. High-precision imaging systems are essential for inspecting PCBs with complex layouts and densely populated components.
Application: A semiconductor equipment manufacturer utilized telecentric lenses in their PCB inspection and alignment systems to achieve precise and accurate imaging of electronic components. These lenses were integrated into machine vision systems equipped with robotic arms for automated inspection and alignment of PCBs during the manufacturing process.
Benefits:
- Telecentric lenses provided distortion-free imaging of PCBs, allowing for accurate detection of defects, misalignments, and soldering anomalies.
- The telecentric imaging setup maintained consistent magnification and depth of field, ensuring sharp focus and accurate measurements across the entire PCB surface.
- By incorporating telecentric lenses into their inspection systems, the semiconductor equipment manufacturer improved production yield, reduced rework costs, and enhanced overall product quality in electronics manufacturing.
These case studies illustrate how telecentric lenses are employed in real-world industrial applications to enhance precision, accuracy, and efficiency in dimensional measurement, inspection, and alignment processes across diverse industries such as automotive manufacturing and electronics production.
Future Trends in Telecentric Optics
As technology continues to advance, several future trends are expected to shape the evolution of telecentric optics:
- Miniaturization and Integration: With the increasing demand for compact and lightweight imaging solutions, telecentric lenses are likely to undergo miniaturization while maintaining or even improving their optical performance. Integrated telecentric optics, combining lenses with other components such as lighting systems or image sensors, may become more prevalent, enabling smaller and more efficient imaging systems for various applications.
- High-Resolution Imaging: Future telecentric lenses are expected to feature higher resolutions to meet the growing demand for detailed imaging in applications such as microscopy, semiconductor inspection, and high-precision metrology. Advancements in lens materials, coatings, and manufacturing techniques may enable the development of telecentric lenses capable of resolving finer details with exceptional clarity and accuracy.
- Adaptive Optics and Active Correction: Telecentric lenses may incorporate adaptive optics technologies to dynamically adjust optical parameters such as focal length, aperture size, and aberration correction in real-time. Active correction mechanisms, such as liquid crystal elements or deformable mirrors, could be employed to compensate for optical aberrations and maintain optimal imaging performance under varying conditions, enhancing the flexibility and versatility of telecentric optics systems.
- Multispectral and Hyperspectral Imaging: Telecentric lenses may be adapted for multispectral and hyperspectral imaging applications, allowing for simultaneous acquisition of spatial and spectral information across multiple wavelength bands. By integrating filters or diffractive elements into the lens design, telecentric optics systems could enable enhanced material identification, chemical analysis, and remote sensing capabilities in fields such as agriculture, environmental monitoring, and biomedical imaging.
- Advanced Metrology and 3D Imaging: Future telecentric lenses may incorporate advanced metrology capabilities, such as phase-shifting interferometry or structured light projection, to enable high-precision 3D imaging and surface profilometry. By combining telecentric optics with 3D imaging techniques, manufacturers could achieve precise measurements of complex geometries, surface roughness, and feature heights in industrial inspection, quality control, and reverse engineering applications.
- Machine Learning and Computational Imaging: Telecentric optics systems may leverage machine learning algorithms and computational imaging techniques to enhance image processing, reconstruction, and analysis capabilities. By intelligently integrating artificial intelligence with telecentric lenses, imaging systems could adaptively optimize imaging parameters, automate defect detection, and extract valuable insights from complex datasets, leading to improved productivity and decision-making in various industries.
Overall, future trends in telecentric optics are expected to focus on enhancing performance, versatility, and intelligence, enabling these specialized lenses to address a broader range of applications and contribute to advances in imaging technology across diverse fields.
Conclusions
In conclusion, telecentric lenses offer unique advantages in scenarios where precision, accuracy, and consistency are paramount. The decision to use telecentric lenses hinges on several key factors:
- Unknown or Variable Object Distance: Telecentric lenses excel in situations where the distance between the lens and the object is uncertain or varies continuously, such as applications involving vibrating conveyor belts or moving objects. Their inherent telecentricity ensures consistent magnification and accurate measurements regardless of the object’s distance from the lens, mitigating the effects of perspective errors.
- Profile Measurement: Telecentric lenses are well-suited for measuring the profile or shape of objects with high precision. By maintaining parallel chief rays and eliminating perspective distortion, these lenses enable accurate profile measurements without the need for complex calibration procedures, making them ideal for applications requiring detailed dimensional analysis.
- Feature Measurement: Telecentric lenses are indispensable for measuring specific features of objects with exceptional accuracy. Whether it’s detecting fine defects, verifying component alignment, or assessing surface roughness, telecentric optics ensure reliable measurement results by preserving consistent magnification and minimizing optical aberrations, even when evaluating objects with varying geometries.
- Evaluation of Objects at Different Distances: In scenarios where objects at different distances need to be continuously evaluated, telecentric lenses provide a reliable solution. Their telecentric imaging characteristics ensure that objects at varying distances within the field of view are imaged with consistent magnification and sharp focus, enabling accurate and reliable analysis across the entire range of distances.
In summary, telecentric lenses are invaluable tools in applications where precise and consistent imaging is essential, offering unparalleled performance in measuring profiles, features, and objects with uncertain or variable distances. By leveraging the unique advantages of telecentric optics, engineers and researchers can achieve enhanced accuracy, efficiency, and reliability in a wide range of industrial, scientific, and imaging tasks.
Related Content
3 Strategies for Field Lens Development and Design
- Explore essential strategies for field lens development, focusing on innovative design techniques that could include elements of telecentric lens design for advanced optical applications.
Design considerations for microlenses and lens arrays
- Gain insights into the design considerations for microlenses and lens arrays. This article likely covers crucial aspects of miniature lens systems, offering perspectives beneficial to understanding the complexities of telecentric lens design.
Telecentric Lens Design FAQs
What distinguishes telecentric lenses from conventional lenses in design?
Telecentric lenses maintain a constant magnification regardless of object distance, unlike conventional lenses.
Why are telecentric lenses crucial in machine vision applications?
They provide consistent, accurate measurements by eliminating perspective errors common in standard lenses.
Can telecentric lenses be customized for specific applications?
Yes, they can be tailored to meet specific requirements in various industrial applications.